JVL's product range nowincludes a series of programmable AC Servo Controllers, AMC20, 21 and 22. These Controllers can be used to control AC motors up to 3kW. They are based on a 16-bit microprocessor and 32-bit signal processor and are characterised by great flexibility in application and control facilities. They can be controlled directly via the built-in RS232 interface, or indirectly via 6 digital inputs. In addition, the Controllers can be supplied with a built-in Profibus. The Controllers can be directly connected to PLCs with axis boards. Up to 255 units can be connected to the same RS232 bus, thus enabling a PC or PLC to function as controller in a multi-axis system.
Using JVL´s programming software, MotoWare, motor power, velocity, torque, etc. can be monitored graphically and comparisons made with previously recorded curves. This facility greatly assists control and troubleshooting.
The Controller's 6 digital inputs refer to 64 user-defined position and velocity references which are stored in registers via the built-in RS232 interface or a Profibus interface (under development). The AMC Controllers can also be velocity controlled by an analog input of +/- 10V. In addition they can be controlled as a step motor system with step-pulse and direction signals.
A special mode of operation provides electronic gearing at any selectable keyed-in ratio (from 0.001 to 9999.999) with a resolution of 1 to 1000.
In the standard model, the programmed values are executed by external signals, while an extended model enables the Controller itself to perform sequential program execution.
8 general-purpose outputs can be configured for example to provide a ready signal when the motor has reached the desired position, or to give an error signal if a condition arises that prevents motor operation.
These Servo Controllers are very easily programmed. For example, various velocity profiles can be set by defining acceleration, deceleration (linear or s-curve) and velocity. The Controllers also have built-in, programmable end-of-travel stops and a zero-point seek function.
For connecting a feedback sensor to the digital feedback loop, the Controllers accept either a balanced or unbalanced signal, e.g. from a standard 2-channel incremental encoder. The Controllers are prepared for master/slave interpolation control in 2 axes.
A new feature in these Controllers is the use of FLASH PROM, which enables the firmware to be changed if required.
All inputs and outputs are galvanically isolated and voltage-overload protected to give high immunity to spurious noise signals. Similarly the Controllers are also protected against thermal overloads and short-circuits. The Controllers have been designed and constructed to fulfil EMC requirements and are CE approved.
Latest Servo Technology in the AMC20 series
AMC20, 21 and 22 are a series of AC Servo Controllers which control AC motors rated up to 3 kW.
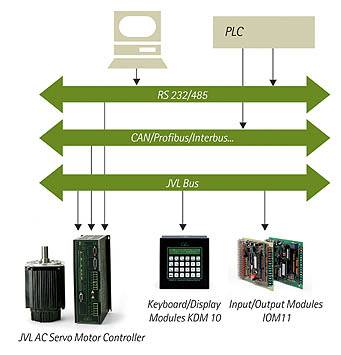
What do you get? Tuning for everyone — choose between 4 tuning methods using AMC2x: Default easy-to-use tuning, PID tuning, Auto tuning and Recipe tuning.
Technically speaking the AMC20 series offer the most advanced technique in the market today for regulation of servo motors — a 7th-order filter.
This filter means that the AMC20 can be adjusted for an extremely high degree of stiffness, a decisive factor in highly dynamic applications.
It also means that the controllers are eminently well-suited for the 3-phase linear servo motors on the market.
Please also note the recipe tuning facility which surpasses any other method of servo control available on the market today — it is simply the ultimate expert tuning.
Using JVL´s programming software - MotoWare - velocity, torque etc., can be monitored graphically and comparisons made with previously recorded curves. This facility greatly assists control and troubleshooting.
In short, the Controllers’ new filter and tuning methods mean: shorter set-up times and better performance, minimum overshoot and positioning errors, and significantly shorter machine cycle times.
Read more about the new technology below...
Features
- Shorter machine cycles
- Short set up time
- Improved performance
- Inexperienced users tune the system easily
- 4 tuning methods: Default, PID, Auto and Recipe tuning
- The most advanced regulation on the market: 7th-order filter
- CAM functions — e.g. for on screwing lids perfectly
- Standard unit: Table positioning with up to 64 positions
- Advanced unit: Freely Programmable controller
- One Compact and Integrated Unit: servo driver, axis controller, mains filter and µPLC in a single compact unit
- Electronic Gearing
- Easy set-up using MotoWare
- CANopen built-in
Latest Servo Technology
JVL has now made it possible for anyone to tune servo systems. Depending on needs and insight, one of the following methods of tuning can be used:
- Default tuning (using load-factor)
- PID tuning
- Auto-tuning
- Recipe tuning - the ultimate expert tuning
Default tuning is well suited for first-time users since there is only one parameter that must be adjusted: the load factor. The larger the inertia of the load, the larger the load factor.
PID tuning is slightly more advanced and involves adjusting 5 different parameters.
Auto-tuning involves an advanced filter. Stiffness, pre-filter, etc., can be specified and an auto-tuning is then carried out.
Recipe tuning is the ultimate expert method of tuning and is even applicable to very complex or undamped systems. A screen display gives the super-user information about the mathematical model of the system, enabling adjustments and optimisation to be made on this basis.
Servo regulation based on 7th-order filter
Many common servo amplifiers are based on 1st or 2nd-order filters (a PID regulator is a 1st-order filter). In contrast, JVL''s latest series is based on a 7th-order filter that offers many clear advantages.
Mechanical systems that are elastic, such as those incorporating drive belts and other non-stiff mechanical components) can be tuned significantly better, offering increased performance.
Linear servo motors are also better utilised. Settling time is brought to a minimum. The AMC20 can be used to control various linear motors. Many linear motor manufacturers do not themselves produce drivers but supply a standard driver together with their products.
The AMC20 provides better performance and in many cases a less expensive solution.
7th-order filtering results in:
- Reduced overshoot
- Mechanical systems that are elastic can be tuned to previously unattainable degrees of stiffness
- Shorter machine cycle times
For information on the MSE series of AC Servo Motors designed for use with the AMC20, 21 and 22 Servo Controllers, click here.