Connect multiple JVL motors through low cost RS422 motors to an existing IOlink, CANopen, Wireless ethernet, Ethernet, DMX512 motor.
Topology One link , One motor for fast response on all motors
Features:
- Connect multiple JVL motors through low cost RS422 motors to an existing IOlink, CANopen , Wireless ethernet, Ethernet, DMX512 motor
- All motor can have MACtalk communication together with MODBUS or CAN communication
- Control multiple motors in daisy chain RS422 network
- Connect multiple JVL motors to an existing Ethernet based network ?
- Save between 10-15% in the investment costs when integrating JVL drives by using IOLink instead of an traditional Ethernet based control network.
- In 90% of the applications where JVL drives are used, the specific axis is used as a setup axis, only requiring a minimal of bandwith and no hard timing requirement
- For the Rockwell environment AOI’s are supported.
Features CAN:
- CAN motor have MACtalk +MODBUS + CAN communication at the same time
- Control motor point to point
- 1Mbit
Features IOLINK module WI1425x:
- By using IO-Link and the new JVL IO-Link gateway a JVL drive (servo or stepper) can be controlled directly from the PLC through an IO-Link Master.
- IOLINK demand gateway module with IOlink M12 5Pin in and 17pin out that connect to stepper or servomotor.
- Motor 1 should have a WI1425 module connected but additional motor can be low cost RS422 MIS*Q9* motors
- Connect multiple motor through a RS422 On same motor connect M12 8pin to motor 2 M12 17pin etc.
- IOLink compatible with Rockwell Armorblock 1732E-8IOLM12R, Siemens and others
- Max 1 Mbit RS422 for only MODBUS and IOLINK motor network.
- Even though the IO-Link based JVL control never was intended to be used in hard timing restrained application, reaction times an be very low.
- The JVL gateway is placed inside a rugged metal tube. 2 Leds indicates the current Link status.
- The metal gateway screws directly into one of the IO-connectors on the motor and an
- IO-Link cable is connected to the other end, that goes directly into the IO-Link master.
- The JVL Gateway is delivered with either 8, 12 or 17Pin connector depending on the
- type of JVL drive used.
- For the MIS motors an added bonus, up to 5 motors can be connected to one IO-Link channel by utilizing multidrop topology on an internal JVL bus, running between the motors.
- For the MAC servo motor range an MAC00-B4 module is required for each motor. Observe that these drives requires one IO-Link channel per. Drive.
- All normal motion functions can be controlled through the IO-Link channel.
- For the MIS Servo stepper series, the Gateway tube connects directly to the 17Pin connector.
Feature Wireless Ethernet:
- Wireless ethernet is build into motor so only antenna is outside. Use the motor internal switch to connect to multiple other Ethernet motor
- MODBUS motor ie 17 pin RS422 MODBUS input and 8 pin MODBUS output to multiple other RS422 motors.
- Use Master with 4-8 channels for point to point to each motor for fastest response. Use daizy chain connection for non timecritical application (The more motors the slower it gets).
- Max 460Mbit RS422 MODBUS for motor with Ethernet
- This Master usually connects directly to the PLC via the Ethernetbus.
|
CANOpen
|
IOLINK
|
Ethernet Wired
|
Wireless Ethernet
|
DMX512
|
J1939
|
Master slave
MODBUS
|
Slave follow MODBUS
|
|

|

|

|

|

|

|

|

|
Hardware Physical layer
|
CAN RS485
|
IOLink 24V seriel
WI1425M12M5TM17T201
|
Ethernet
|
Wifi+Profinet/EthernetIP
ModbusTCP/UDP
|
RS485 or
RS422
|
CAN
RS485
|
RS422
duplex
|
RS422
duplex
|
JVL MACmotor module
|
MAC00-FC41
|
MAC00-Ex41: WI1425M12M5TM17T201
MAC00-B41: WI1425M12M5TM12T201
MAC00-B4 : WI1425M12M5TM8T501
|
-
|
MAC00-WI ( EthernetIP)
MAC00-WP (Profinet)
MAC00-WM ( MODBUS TCP/UDP)
|
MAC00-FS4
|
n/a
|
MAC00-B4
MAC00-B41
MAC00-Ex4
|
|
JVL motor MIS/SMC66/85
|
MIS/SMC*P6*
|
WI1425M12M5TM17T201+
MIS/SMC*Q5/Q9
|
MIS/SMC*
E2 Ethercat+MOSBUS
E3: Ethernet/IP+MODBUS
E4:Powerlink+RS422
E5: Modbus TCP+MODBUS
E6: Profinet+SSI
|
MIS/SMC
WI ( EthernetIP)
WP(Profinet)
WM ( MODBUS TCP/UDP)
|
MIS/SMC
*Q5/Q9
|
MIS/SMC
*P6*
|
MIS/SMC
*Q5/Q9
|
MIS/SMC
*Q5/Q9
|
AIO support
|
|
PDO Max5 motors with multidrop
|
|
|
|
|
|
|
Max number of nodes. Address range
|
255
|
255
|
|
65535
|
512
|
|
|
|
Syncronization
|
Yes
|
No
|
|
|
|
|
|
|
Cyclic Sync cycletimes
|
|
|
|
|
|
|
|
|
Minimum cycle time
|
|
|
|
1mS for 5 Reg
|
|
|
|
|
Drive profile
|
CiA402
|
|
|
Planned Profidrive
|
No
|
|
|
|
Daicychain
|
Yes 5pin M 5p Female
|
Yes
|
|
Yes Wireless ethernet in.
Ethernet or MODBUS out
|
|
|
|
|
Communications speed
|
|
460 kbit
|
|
|
9.6 to
921kbit
|
|
|
|
Reaction time
|
|
|
|
|
|
|
|
|
Read & write IO+reg in motor
|
Yes
|
Yes
|
|
|
Yes
|
Yes
|
Yes
|
Yes
|
JVL AOI
|
|
Yes Rockwell
|
|
|
|
|
|
|
JVL Function Block
|
|
|
|
Yes Siemens Profinet
|
|
|
|
|
JVL Example
|
Yes Beckhoff
|
|
|
|
|
|
|
|
Motor suppported
|
MIS*Q5*/*Q9*
|
|
|
|
|
|
|
|
Protocol supported
|
|
|
|
|
|
|
|
|
User organization
|
Link
|
Link
|
|
|
Link
|
Link
|
Link
|
Link
|
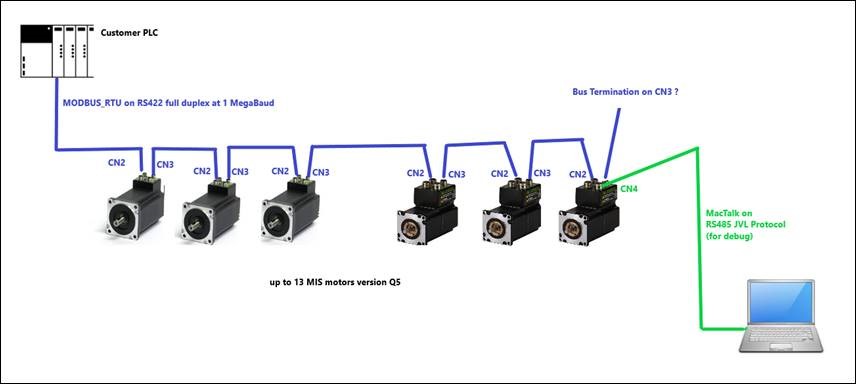